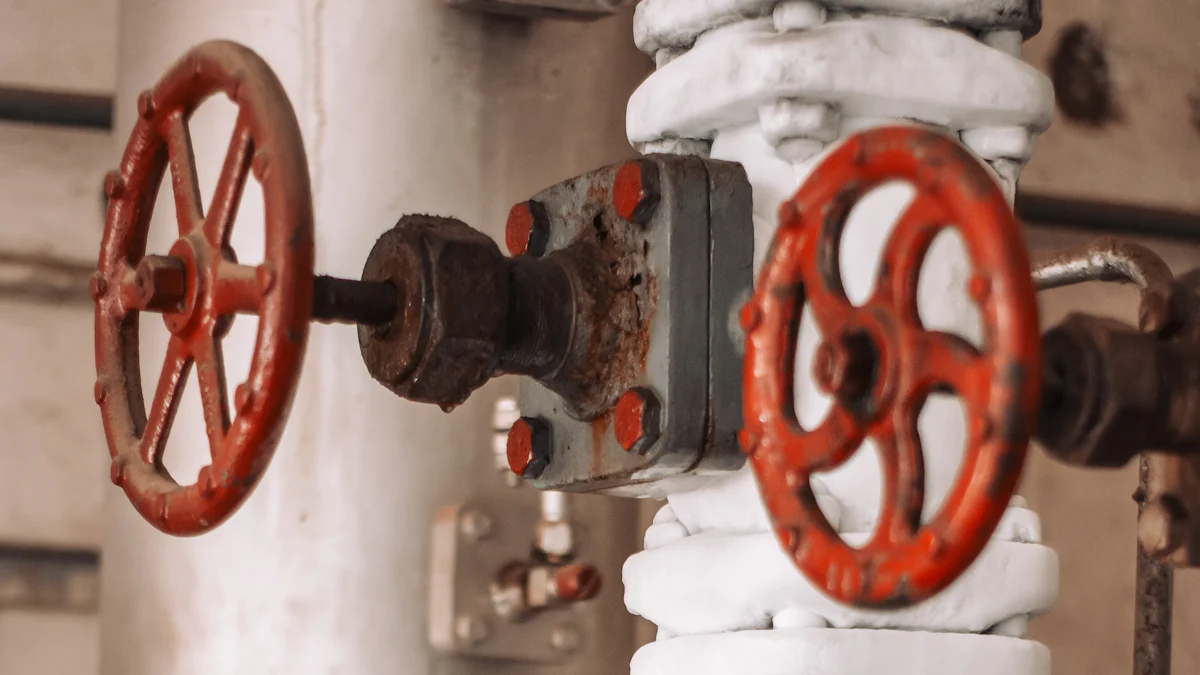
A solenoid valve is an electromechanical device that controls the flow of fluids or gases with precision. You encounter these valves in countless systems, from industrial machinery to household appliances. Their ability to ensure efficient and safe operation makes them indispensable across industries. By understanding how these valves function and their specifications, you can make informed decisions when selecting the right one for your needs. This knowledge helps you optimize performance and maintain safety in your applications.
Key Takeaways
- Understand the material and construction of solenoid valves to ensure durability and compatibility with your specific application.
- Choose between direct-acting and pilot-operated valves based on your system’s pressure requirements and flow rate needs.
- Evaluate voltage and power requirements carefully to select energy-efficient solenoid valves that align with your operational goals.
- Always check the pressure and temperature ratings of solenoid valves to prevent failures and ensure safe operation in your systems.
- Select the appropriate seal material based on the type of fluid being controlled to enhance reliability and prevent leaks.
- Regular maintenance, including inspections and timely replacement of worn components, is crucial for extending the lifespan of solenoid valves.
- Consult technical datasheets to make informed decisions and avoid common mistakes when selecting solenoid valves for your applications.
Key Specifications of Solenoid Valves
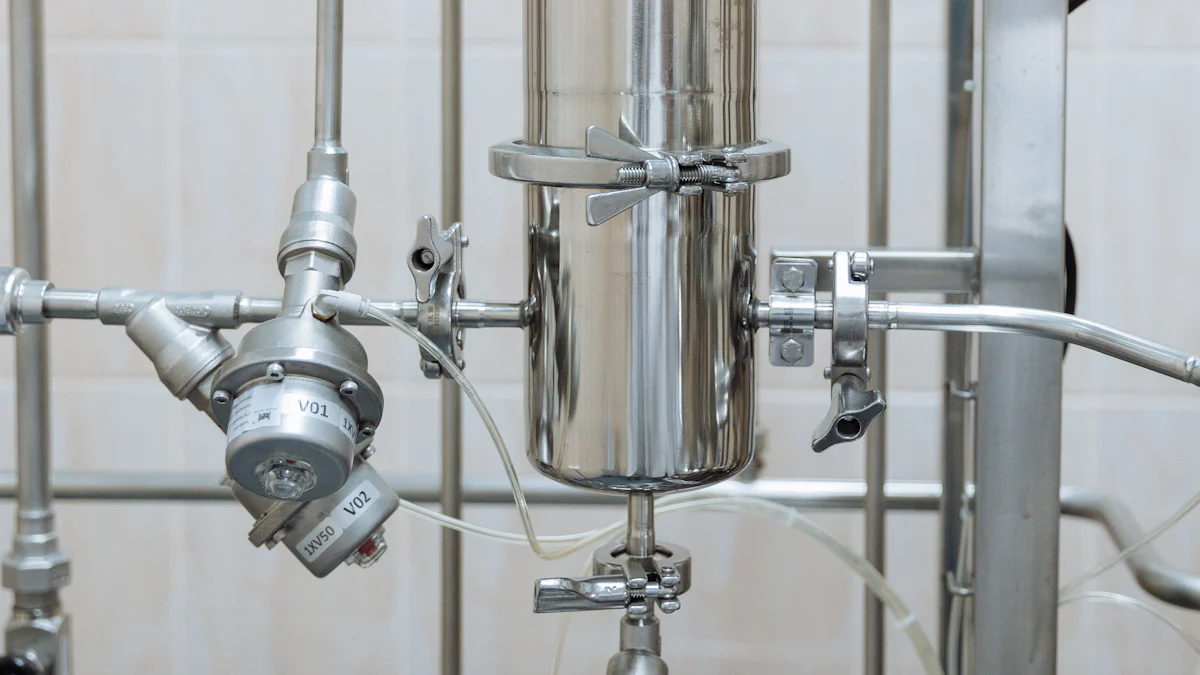
Material and Construction
Common materials (e.g., stainless steel, brass, plastic) and their suitability for different environments.
The material of a solenoid valve plays a critical role in its performance and durability. Stainless steel, brass, and plastic are the most common materials used. Stainless steel offers excellent resistance to corrosion, making it ideal for harsh environments or applications involving aggressive chemicals. Brass, on the other hand, works well in general-purpose applications due to its strength and cost-effectiveness. Plastic valves are lightweight and suitable for non-corrosive fluids or low-pressure systems. When selecting a valve, you must consider the environment and the type of fluid it will control.
Importance of corrosion resistance and durability.
Corrosion resistance ensures the longevity of a solenoid valve, especially in demanding conditions. A valve exposed to corrosive substances without proper material selection may fail prematurely. Durability is equally important, as it determines how well the valve withstands wear and tear over time. Choosing a valve with high-quality construction reduces maintenance needs and ensures reliable operation. Always prioritize materials that align with your application’s requirements to avoid unnecessary replacements.
Valve Type
Direct-acting vs. pilot-operated valves and their operational differences.
Solenoid valves come in two main types: direct-acting and pilot-operated. Direct-acting valves operate without relying on external pressure. They open or close the flow path directly when energized, making them suitable for low-pressure systems or when precise control is needed. Pilot-operated valves, however, use system pressure to assist in opening or closing. These valves are more efficient in high-pressure systems and handle larger flow rates. Understanding these differences helps you choose the right valve for your specific application.
Examples of use cases for each type.
Direct-acting solenoid valves are commonly used in medical devices, such as oxygen concentrators, where precision and reliability are crucial. They also work well in small-scale water systems. Pilot-operated valves are often found in industrial settings, such as manufacturing plants or HVAC systems, where they manage higher pressures and larger volumes of fluid. By matching the valve type to your system’s needs, you ensure optimal performance.
Voltage and Power Requirements
AC vs. DC voltage options and their implications.
Solenoid valves operate on either AC or DC voltage. AC-powered valves are widely used in industrial applications due to their ability to handle higher power loads. DC-powered valves, however, offer quieter operation and greater energy efficiency. They are often preferred in portable or battery-operated systems. When choosing a valve, you must verify the voltage compatibility with your system to avoid operational issues.
Power consumption considerations for energy efficiency.
Energy efficiency is an important factor, especially in systems that run continuously. Solenoid valves with lower power consumption reduce energy costs and minimize heat generation. Some modern valves feature energy-saving coils that maintain functionality while using less power. Evaluating the power requirements of your valve ensures that it aligns with your system’s efficiency goals.
Pressure and Temperature Ratings
Maximum and minimum pressure ratings for safe operation.
Pressure ratings define the operational limits of a solenoid valve. Every valve has a maximum and minimum pressure it can handle safely. Exceeding these limits can lead to valve failure or system damage. You must check the pressure range specified by the manufacturer to ensure compatibility with your system. For example, valves designed for high-pressure systems often feature reinforced construction to withstand intense forces. On the other hand, low-pressure valves are optimized for precision in delicate applications. Always match the valve’s pressure rating to your system’s requirements to maintain safety and efficiency.
Temperature compatibility for different fluids and environments.
Temperature plays a critical role in the performance of a solenoid valve. Each valve is designed to operate within a specific temperature range. Using a valve outside its temperature limits can cause material degradation or malfunction. For instance, high-temperature environments may require valves made from heat-resistant materials, while low-temperature systems need components that prevent freezing. Additionally, the type of fluid being controlled affects temperature compatibility. Hot steam demands a valve with robust thermal resistance, while cold liquids require materials that maintain flexibility. Understanding these factors ensures reliable operation in any environment.
Port Size and Flow Rate
How port size affects flow capacity.
The port size of a solenoid valve directly impacts its flow capacity. Larger ports allow more fluid to pass through, increasing the flow rate. Smaller ports restrict flow, making them suitable for precise control in low-flow applications. When selecting a valve, you should consider the size of the ports in relation to your system’s flow requirements. A mismatch can lead to inefficiencies, such as insufficient flow or excessive pressure drops. Properly sized ports ensure smooth and consistent operation, optimizing the performance of your system.
Calculating flow rate requirements for specific applications.
Determining the flow rate is essential for choosing the right solenoid valve. Flow rate refers to the volume of fluid passing through the valve over a specific period. To calculate it, you need to know the system’s pressure, the fluid’s properties, and the desired flow speed. Manufacturers often provide flow coefficient (Cv) values to help you estimate the valve’s capacity. By using these values, you can select a valve that meets your application’s demands without overloading the system. Accurate calculations prevent operational issues and enhance efficiency.
Seal Material Compatibility
Common seal materials (e.g., NBR, EPDM, PTFE) and their chemical resistance.
Seal materials play a vital role in the functionality of a solenoid valve. Common options include NBR (nitrile rubber), EPDM (ethylene propylene diene monomer), and PTFE (polytetrafluoroethylene). Each material offers unique chemical resistance properties. NBR works well with oils and fuels but may degrade when exposed to strong acids. EPDM resists water and steam but is unsuitable for petroleum-based fluids. PTFE provides excellent resistance to chemicals and high temperatures, making it ideal for aggressive environments. Selecting the right seal material ensures durability and prevents leaks.
Matching seal materials to the type of fluid being controlled.
The fluid type determines the appropriate seal material for a solenoid valve. For example, water systems often use EPDM seals due to their compatibility with moisture. Oil-based fluids require NBR seals for optimal performance. In chemical processing, PTFE seals are preferred for their ability to withstand corrosive substances. Using the wrong seal material can lead to premature wear, leaks, or contamination. By matching the seal material to the fluid, you enhance the valve’s reliability and extend its lifespan.
Applications of Solenoid Valves
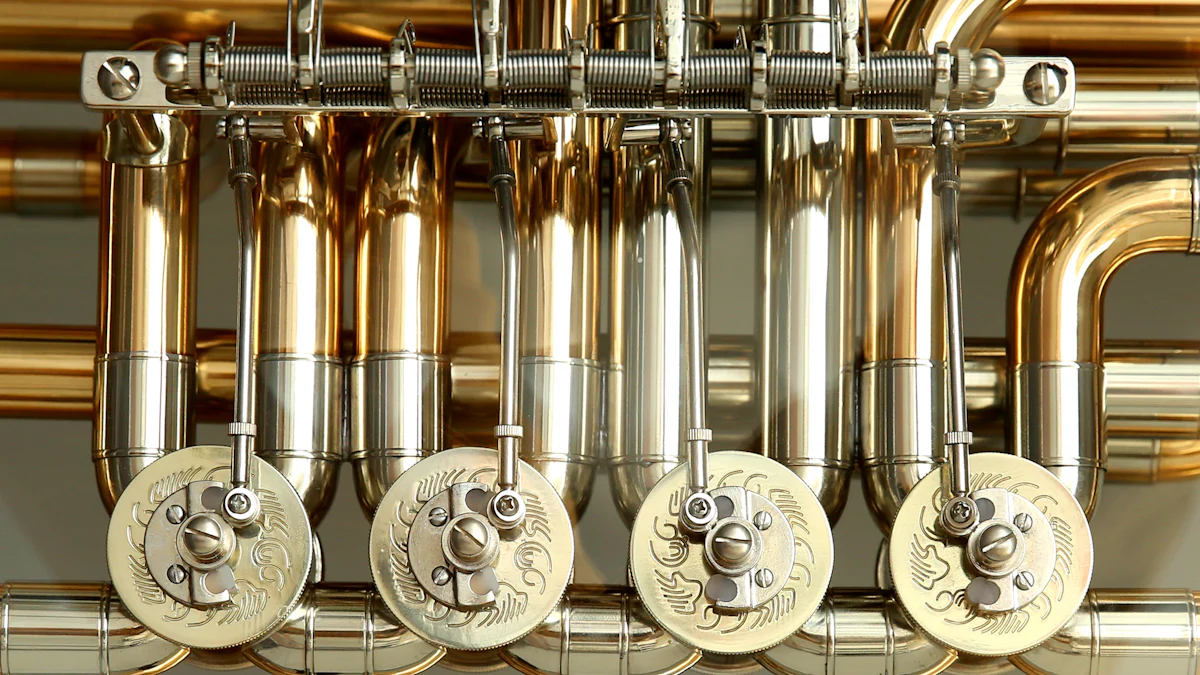
Industrial Applications
Use in manufacturing processes, oil and gas, and chemical industries.
You will find solenoid valves playing a vital role in industrial operations. These valves control the flow of fluids and gases in manufacturing processes, ensuring precision and safety. In the oil and gas sector, they regulate the movement of crude oil, natural gas, and other substances through pipelines and equipment. Chemical industries rely on these valves to handle corrosive or hazardous materials, maintaining strict control over their processes. Their ability to operate quickly and reliably makes them indispensable in these demanding environments.
Examples of controlling steam, gas, or hazardous fluids.
Solenoid valves excel in managing steam, gas, and hazardous fluids. For instance, they control steam flow in power plants, ensuring efficient energy production. In gas distribution systems, they regulate the supply of natural gas to prevent leaks or overpressure. When dealing with hazardous fluids, such as acids or toxic chemicals, these valves provide precise control to minimize risks. Their robust design and material compatibility make them suitable for handling challenging substances safely.
HVAC Systems
Role in regulating heating, cooling, and ventilation systems.
In HVAC systems, solenoid valves help you maintain comfortable indoor environments. They regulate the flow of refrigerants, water, or air within heating, cooling, and ventilation systems. By controlling these elements, the valves ensure that your HVAC system operates efficiently and maintains the desired temperature and air quality. Their quick response time allows for precise adjustments, which is essential for energy savings and consistent performance.
Examples of solenoid valves in air conditioning units.
Air conditioning units often use solenoid valves to manage refrigerant flow. These valves open and close to control the cooling cycle, ensuring that the system operates at optimal efficiency. For example, they can stop the refrigerant flow when the desired temperature is reached, preventing unnecessary energy consumption. Their reliability and precision make them a key component in modern air conditioning systems, helping you achieve both comfort and cost savings.
Medical Equipment
Use in devices like oxygen concentrators and dialysis machines.
Medical devices depend on solenoid valves for their accuracy and reliability. In oxygen concentrators, these valves control the flow of oxygen to ensure patients receive the correct dosage. Dialysis machines use them to regulate the movement of fluids, maintaining the precise balance required for effective treatment. Their compact size and ability to handle delicate operations make them ideal for medical applications where precision is critical.
Importance of precision and reliability in medical applications.
In medical settings, precision and reliability are non-negotiable. Solenoid valves deliver consistent performance, ensuring that medical devices function as intended. A malfunction in these valves could compromise patient safety, so their design prioritizes durability and accuracy. By using high-quality solenoid valves, you can trust that medical equipment will operate smoothly, providing the care and support patients need.
Automotive Industry
Applications in fuel systems, emission controls, and hydraulic systems.
In modern vehicles, solenoid valves play a crucial role in ensuring efficient and precise operation. You will find these valves in fuel systems, where they regulate the flow of fuel to the engine. By controlling the fuel injection process, they help optimize combustion and improve engine performance. In emission control systems, solenoid valves manage the flow of exhaust gases, reducing harmful emissions and ensuring compliance with environmental standards. Hydraulic systems in vehicles, such as those used in automatic transmissions or braking systems, also rely on solenoid valves to control fluid pressure and flow. These applications highlight the importance of solenoid valves in maintaining vehicle safety, efficiency, and environmental responsibility.
Examples of solenoid valves in modern vehicle designs.
Automotive manufacturers integrate solenoid valves into various components to enhance functionality. For example, in advanced fuel injection systems, solenoid valves ensure precise timing and delivery of fuel, improving fuel economy and reducing emissions. In hybrid and electric vehicles, these valves manage cooling systems by regulating the flow of coolant to maintain optimal battery temperatures. Another example is the use of solenoid valves in turbochargers, where they control airflow to boost engine power. These examples demonstrate how solenoid valves contribute to the innovation and performance of modern vehicle designs.
Water and Wastewater Management
Use in irrigation systems, water treatment plants, and plumbing.
Solenoid valves are essential in water and wastewater management systems. In irrigation systems, they control the flow of water to specific areas, ensuring efficient water distribution and conservation. You can program these valves to operate automatically, making them ideal for agricultural and landscaping applications. In water treatment plants, solenoid valves regulate the flow of chemicals and water through filtration and purification processes. This ensures clean and safe water for consumption. Plumbing systems also benefit from solenoid valves, which manage water flow in residential and commercial buildings. Their ability to operate quickly and reliably makes them indispensable in these applications.
Examples of controlling water flow and pressure.
You can see solenoid valves in action in drip irrigation systems, where they precisely control water flow to individual plants, reducing waste and promoting healthy growth. In municipal water treatment facilities, solenoid valves manage the flow of chlorine and other disinfectants, ensuring proper water quality. In plumbing systems, these valves control water pressure in appliances like washing machines and dishwashers, preventing leaks and maintaining efficiency. These examples illustrate how solenoid valves contribute to effective water management and resource conservation.
Choosing the Right Solenoid Valve
Matching Specifications to Application Needs
Steps to evaluate application requirements (e.g., fluid type, pressure, temperature).
Selecting the right solenoid valve begins with understanding your application’s specific needs. Start by identifying the type of fluid the valve will control. Fluids like water, oil, or gas have unique properties that require compatible materials and designs. Next, determine the operating pressure and temperature ranges. High-pressure systems demand valves with reinforced construction, while extreme temperatures may require specialized materials. Evaluate the flow rate requirements by calculating how much fluid needs to pass through the valve within a given time. These steps ensure the valve aligns with your system’s demands.
Importance of consulting technical datasheets.
Technical datasheets provide essential information about a solenoid valve’s capabilities. These documents include details like pressure ratings, temperature limits, and material compatibility. Reviewing this data helps you confirm whether the valve meets your application’s requirements. Manufacturers often include performance curves and flow coefficients (Cv values) to guide your selection process. By consulting these datasheets, you reduce the risk of choosing an incompatible valve and ensure optimal performance in your system.
Common Mistakes to Avoid
Overlooking compatibility with fluid or environmental conditions.
Ignoring fluid or environmental compatibility can lead to valve failure. For example, using a valve with seals that degrade in the presence of certain chemicals may cause leaks. Similarly, selecting a valve made from non-corrosion-resistant materials for a humid or corrosive environment shortens its lifespan. Always verify that the valve’s materials and design match the fluid and environmental conditions of your application.
Choosing the wrong valve type for the application.
Using the wrong type of solenoid valve can compromise your system’s efficiency. Direct-acting valves may struggle in high-pressure systems, while pilot-operated valves may not function properly in low-pressure environments. Misjudging the valve type can result in operational issues, such as inconsistent flow or system malfunctions. Understanding the differences between valve types ensures you select the one best suited for your needs.
Maintenance and Longevity Tips
Regular inspection and cleaning to prevent clogging or wear.
Routine maintenance keeps your solenoid valve functioning efficiently. Inspect the valve regularly for signs of wear, corrosion, or debris buildup. Cleaning the valve prevents clogging, which can restrict fluid flow and reduce performance. Use appropriate cleaning agents that do not damage the valve’s materials. Regular maintenance extends the valve’s lifespan and minimizes downtime in your system.
Importance of replacing worn-out seals and components.
Seals and other components wear out over time due to constant use. Worn seals can cause leaks, while damaged components may affect the valve’s operation. Replacing these parts promptly prevents further damage and ensures the valve continues to perform reliably. Keep spare parts on hand to address issues quickly. Proactive replacement of worn components saves you from costly repairs and system failures.
Understanding solenoid valve specifications is essential for achieving optimal performance in your systems. These valves serve a wide range of applications, from industrial processes to medical devices, highlighting their versatility and importance. Selecting the right valve requires careful evaluation of your specific needs, including fluid type, pressure, and environmental conditions. By making informed choices and consulting experts when necessary, you ensure reliability, efficiency, and safety in your operations. Take the time to assess your requirements thoroughly to maximize the benefits these valves offer.
FAQ
What is a solenoid valve, and how does it work?
A solenoid valve is an electromechanical device that controls the flow of liquids or gases. It uses an electromagnetic coil to open or close a valve mechanism. When you energize the coil, it creates a magnetic field that moves a plunger or armature, allowing fluid to pass through or blocking its flow.
How do I choose the right solenoid valve for my application?
To select the right solenoid valve, you need to evaluate your system’s requirements. Consider the type of fluid, operating pressure, temperature range, and flow rate. Check the valve’s material compatibility with the fluid and environment. Review the technical datasheet for specifications like voltage, seal material, and port size.
What are the differences between direct-acting and pilot-operated solenoid valves?
Direct-acting valves operate without external pressure. They open or close the flow path directly when energized, making them suitable for low-pressure systems. Pilot-operated valves use system pressure to assist in operation. These valves handle higher pressures and larger flow rates, making them ideal for industrial applications.
Can solenoid valves handle high temperatures or corrosive fluids?
Yes, but you must choose the right materials. For high temperatures, look for valves made from heat-resistant materials like stainless steel or PTFE seals. For corrosive fluids, select valves with chemical-resistant materials such as PTFE or EPDM. Always verify the valve’s temperature and chemical compatibility with your application.
How do I calculate the flow rate for a solenoid valve?
To calculate flow rate, you need to know the system’s pressure, fluid properties, and desired flow speed. Use the valve’s flow coefficient (Cv) provided by the manufacturer. The Cv value helps you estimate how much fluid the valve can handle under specific conditions.
What maintenance does a solenoid valve require?
Regular maintenance ensures optimal performance. Inspect the valve for wear, corrosion, or debris buildup. Clean the valve to prevent clogging. Replace worn-out seals and components promptly. Following these steps extends the valve’s lifespan and reduces downtime.
Are solenoid valves energy-efficient?
Many solenoid valves are energy-efficient, especially those with low power consumption or energy-saving coils. DC-powered valves often consume less energy than AC-powered ones. Choosing an energy-efficient valve reduces operational costs and minimizes heat generation.
Can solenoid valves be used in medical devices?
Yes, solenoid valves are widely used in medical devices. They control fluid flow in equipment like oxygen concentrators and dialysis machines. Their precision and reliability make them essential for maintaining patient safety and ensuring accurate operation.
What happens if I use the wrong solenoid valve for my system?
Using the wrong valve can lead to operational issues. For example, a valve incompatible with the fluid may degrade or leak. A mismatched pressure rating could cause system failure. Always match the valve’s specifications to your system’s requirements to avoid problems.
How long do solenoid valves typically last?
The lifespan of a solenoid valve depends on factors like material quality, operating conditions, and maintenance. High-quality valves with proper care can last several years. Regular inspection and timely replacement of worn components help extend their service life.
Post time: Dec-31-2024